Tubular solders Multicore Solders designed for various applications, including soldering of printed circuit boards of electronic equipment and construction products.
Manufactured tubular solders with different percentages and different types of flux and of different diameters.
The composition of the solder
For the manufacture of tubular solders by Multicore Solders are used only high-purity alloys with a minimum amount of impurities that meet the requirements of all major national and international standards, including QQ-S-571E and J-STD-006A. Solders can be supplied with different types of alloys:
Traditional alloys
Traditionally in our country used tin-lead eutectic solder or close to them:
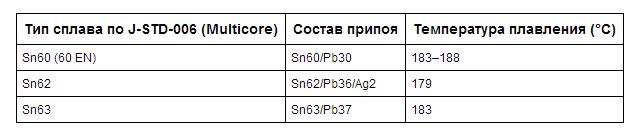
For soldering SMD components recommended solders tubular diameter in the range of 0.46 - 1.0 mm. Especially for soldering tiny chip components supplied tubular solders based alloy Sn62 / Pb36 / Ag2 diameter of 0.46 and 0.56 mm. Silver added to prevent migration of the silver used in the production of chip components, solder and to increase the strength of the solder joint. For other applications are recommended alloys Sn60 / Pb30 (analogue POS-61) and Sn63 / Pb37.
Lead-free alloys
The requirement of time - lead-free alloys are widely used in the manufacture of tubular solders:
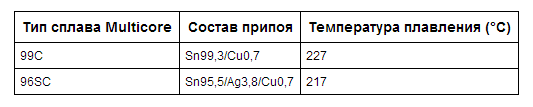
Lead-free alloy 99c on the main characteristics is a close analogue of the traditional alloy Sn60, which allows to replace it without significant changes in the process.
Special alloy brazing Aluminium Company Multicore Solders produces tubular solders for the soldering of structural and manufacturing lamps:

This alloy has high corrosion resistance in comparison with conventional tin-zinc solders.
Flux
Most solders tubular Multicore Solders used based fluxes chemically purified rosin. Such fluxes have a small amount of residues compared to the conventional rosin and higher activity. Removal of flux residues X39, Crystal Crystal 400 and 502 after brazing is unnecessary, since Flux residues have resistance to moisture and temperature during operation. Remains of data flux after soldering without washing withstand the surface insulation resistance standards Bellcore TR-NWT-000078 Issue 3 (December 1991) and IPC protocols 1, 2 and 3 classes.
When choosing the type of flux should be considered compatible flux tube is part of the solder flux for soldering and a group composed of solder pastes, fluxes mutual reaction of different manufacturers may result in a deterioration of the electrical parameters of the product or complicate the cleaning process. Fluxes X39, Crystal Crystal 400 and 502 are fully compatible with solder paste RM92, CR32, CR36, MP200, LF318 and LF320, as well as all types of soldering fluxes for a group that does not require washing, the firm Multicore Solders. Compatible fluxes confirmed by laboratory tests.
Soldering surfaces with poor solderability apply solder flux tube Hydro X, allows you to effectively oxidized solder on copper, brass, nickel and even mild steel. Flux Hydro X has the unique ability soldering surfaces with very poor solderability due to the use of highly active halogen activators. Tubular solder flux Hydro X is fully compatible with solder paste WS200 and WS300, and flux for soldering Group Hydro X / 20.